一、技术简介
液压模板外模采用可行走整体式液压模板,由轨道、行走台车、模板三部分组成,内模为抽拉结构,通过上下对拉结构进行加固。每套外模共设二个液压泵站,每侧模板配一个,给各种油缸与马达提供动力来源。单侧配置的执行元件分别为脱模模油缸3件,顶升油缸8个,横向平移油缸4件,马达4个。其中脱模油缸行程为200mm,以满足模板与外伸钢筋不干涉的要求。垂直顶升油缸行程240mm,使模板上下升降运动,用于实现模板的高低调整。横向平移油缸行程为1.1米,用于整体模板的水平移动,实现模板的开模合模。
液压模板组装完成后,根据所预制的梁长选择调节块,首先调整侧模,操作上下移动液压油缸对侧模标高进行粗调,比设计标高稍低,同时保证腹板模板倾斜度符合要求。操作左右平移油缸将侧模向内移动确保侧模到中心线距离满足设计要求。通过上下移动油缸和地脚支撑对模板标高进行精确调整,侧模下部应与底模接触。通过下对拉杆时侧模顶紧底模,固定顶托。内模拼装完成后,待底腹板钢筋安装完毕通过龙门吊吊入外模内。
在预制过程中,外模是一个整体,只需将外模通过轨道行走至下一个台座进行简单的调整后即可开始预制下一片箱梁。
二、试点项目和单位
试点项目:泉州市二重环湾快速路(晋江段)新建工程一期工程A1标
试点单位:山东省路桥集团有限公司
三、特点和优点
(一)液压模板不仅可以节省人工成本,同时施工速度快、效率高。按照传统模板拆卸到拼装完成至少需要8个工人8小时,而采用液压整体式行走模板,从拆模到行驶到下一台座,需要2个工人最多10分钟(行走电机速度为4m/min)。
(二)模板整体移动,不需要单块拼装,拆装都不需要龙门吊,安全系数提高。将各阶段拼装后,使模板形成一个整体,后续箱梁预制施工都是一个整体一次性完成,无需中间过程拆卸和拼装。而且通过液压系统提供动力,可以纵向、水平、竖直方向自行沿固定轨道行走,不需龙门吊协助,施工安全系数高。
(三)台座数量少,可减少占地面积。与传统工艺相比,台座数量可相应减少50%,减少土地占用,符合绿色施工理念。
(四)模板平整、拼缝严密,尺寸精度高,极大的提高了预制箱梁的外观质量。传统模板由各种节段组成,无论节段间的拼缝如何填充密实,都会留下一道道竖向接缝。而液压整体式模板节段间焊接后打磨平整,梁体腹板是一个整体的平面,不存在拼缝,外观质量得到很大的提高。
四、附图

标准断面图
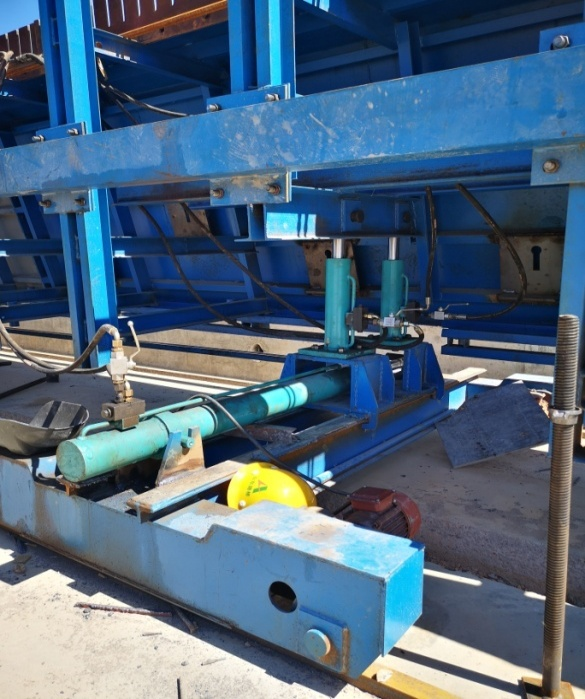

液压系统

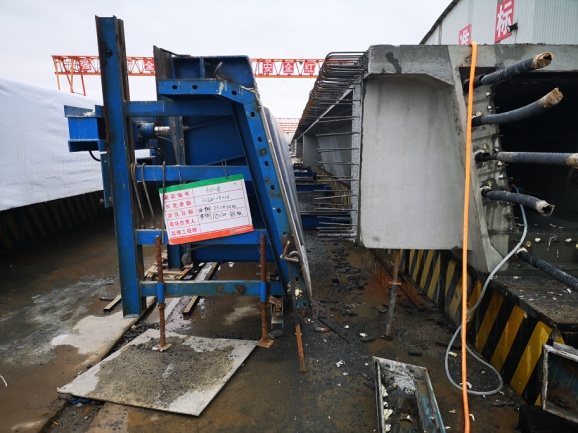
模板脱模横移
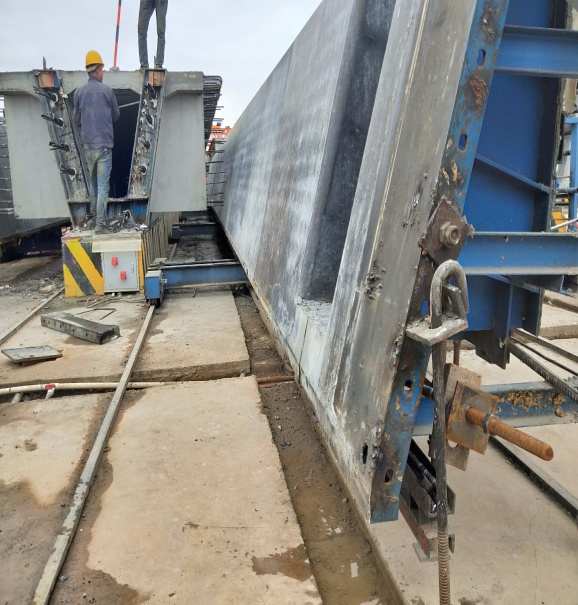
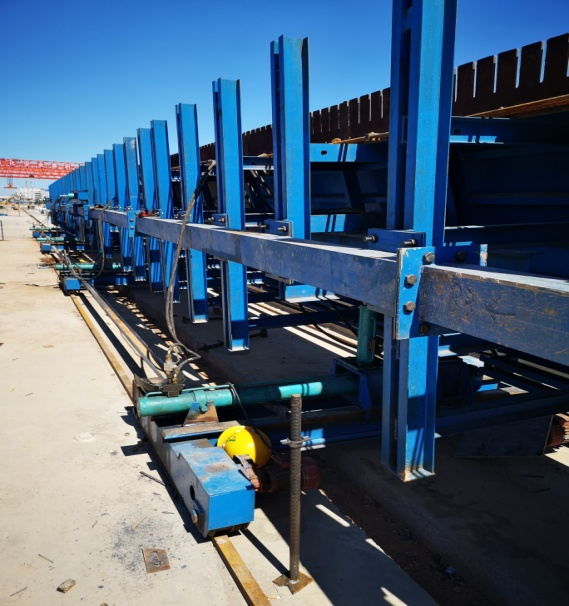
外模行走纵移至下一台座
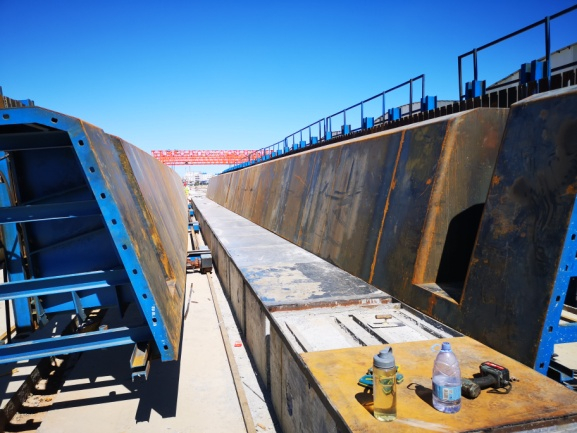
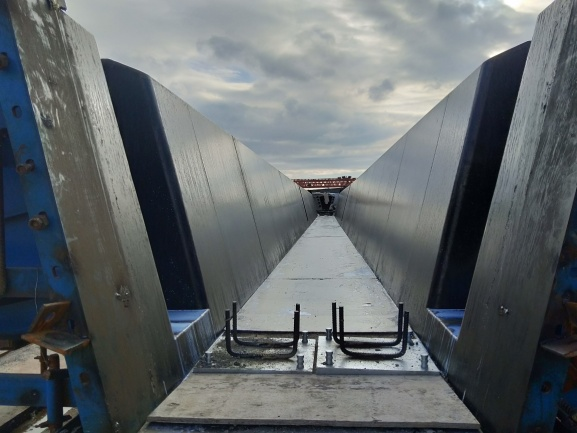
精确定位
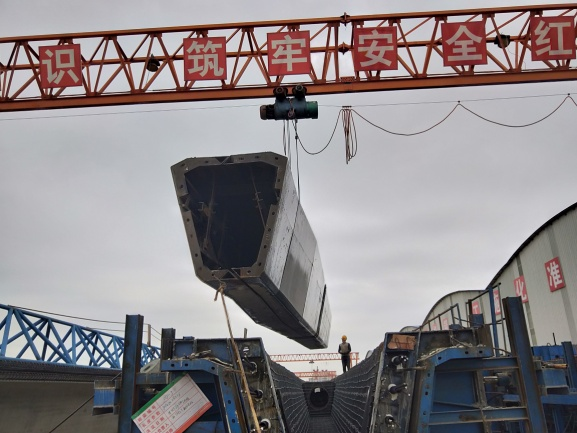

芯模安装固定
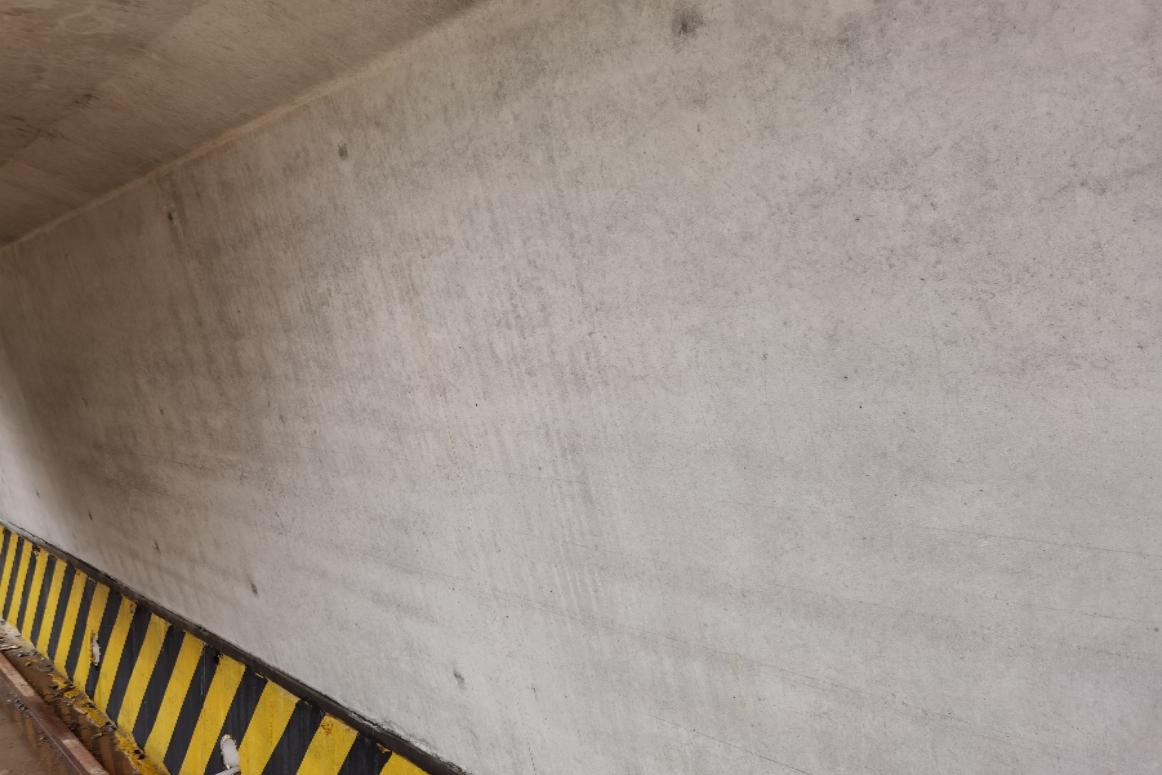
有效减少模板拼接错台质量通病